A Bit About Steel Siding
- John@LiteHouse
- Mar 15, 2023
- 4 min read
Updated: Aug 22, 2023
History of Steel Siding
Sheet metal and steel siding was patented in 1903. Sears, Roebuck & Company began offering embossed steel siding in stone and brick designs in the 1930s.
During this time, rural North America saw a shift in farming practices from animal-driven to equipment-dependent, necessitating a quick and economical method of constructing outbuildings to house machinery and supplies. One popular result was structures known as barns, which used debarked, debranched sections of tree trunks to support the exterior walls and roof, which were composed of galvanized, corrugated, or grooved steel sheet. The buildings proved to be extremely durable as they still cover the rural American landscape today. Barn designs have since evolved based on aesthetics and available resources, but most still include steel as a cladding material, and many modern barns are built almost entirely of steel.
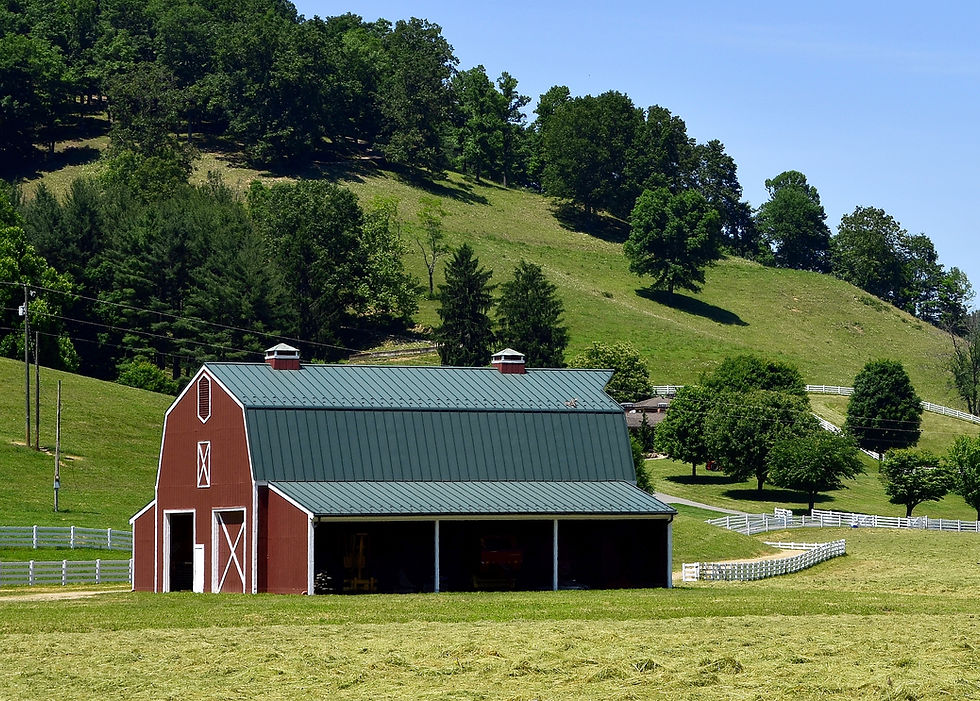
Properties of steel cladding
Modern steel siding can be made of galvanized steel or stainless steel - a difference that affects its susceptibility to corrosion. Galvanized steel is coated with a thin layer of corrosion-resistant zinc that can wear away over time due to moisture-induced rust that can penetrate a deep scratch caused by environmental or mechanical damage. Chromium in stainless steel serves the same purpose as zinc in galvanized steel, except that the chromium is mixed throughout the steel. As a result, the chromium cannot wear away, making stainless steel comparatively more resistant to corrosion than galvanized steel.
Steel, which is designed to be corrosion-resistant, combined with the application of epoxies and corrosion-inhibiting coatings, has allowed steel siding to compete with aluminum, which is cheaper, lighter, and naturally corrosion-resistant. Additionally, homeowners can now choose from a huge variety of steel siding patterns and colors, some of which closely resemble traditional residential siding, such as beveled wood siding, cedar shingles, brick, and even stone. Builders and homeowners can choose from a wide variety of top coat colors and textures, some pre-painted and others that use vinyl, polyvinyl or a proprietary coating product with similar durability.
Options in steel cladding
Homeowners can also choose from the following steel alternatives:
Seamless steel includes a variety of steel cladding that is cut to the exact length of the building, eliminating unsightly seams that allow moisture to penetrate and high winds to dislodge individual panels. Seamless steel contributes to a tighter building envelope, which lowers energy bills and lowers greenhouse gas emissions.
Steel log siding replicates the rustic look of a log without any seams or vulnerability to rodents, decay, or other problems inherent in log homes (some of which are explained in InterNACHI's Inspecting Log Homes article).
For added strength and rigidity, builders often use corrugated steel siding, which comes in a variety of profiles, from large "barn roof" sizes that provide dramatic light and shade to smaller profiles used for patios. However, corrugated steel is more difficult to clean and attaching signs and other items can be difficult.
Advantages
Steel siding has also begun to compete with aluminum in the residential siding market for the following reasons:
strength and durability. Steel can withstand impacts from baseballs and tree branches better than weaker siding materials such as vinyl, wood, brick and aluminum. In areas prone to severe weather, steel is desirable for its resistance to large hail, wind-blown debris and bitter cold. Steel cladding also does not become brittle with age;
little maintenance required. Steel siding requires relatively little maintenance as most accumulated dirt and debris is washed away by the rain. A garden hose can also be used and the steel is strong enough to withstand the force of a pressure washer when extra strength is required;
resistance to insects and rot. Metal siding is inorganic and rot-resistant. Insects and rodents are not attracted to steel and cannot penetrate it;
fire resistance. Steel cladding will not ignite or burn and will not melt under normal circumstances. Steel's melting point is around 2,500 °F (1,370 °C), so it is unlikely to melt in a house fire, while aluminum's melting point of 1,220 °F (660 °C) means it will succumb in a fire. So if a grill gets too close to a house's steel siding, for example, the occupants are likely to be safe; and
color preservation. Steel will not fade, unlike aluminum siding, which fades over time and weathers to a chalky texture.
Disadvantages
Homeowners should balance the advantages of steel siding with the following disadvantages, which continue to relegate steel to marginal siding material:
corrosion (rust) caused by long-term exposure to moisture. Corrugated steel showing signs of rust Rust is a problem that is unique to steel and iron and can be a serious problem in coastal and humid areas. Look for red, orange, or brown pits or scales that allow moisture, insects, or dirt to enter the building. For more information on rust treatment and prevention, see the InterNACHI article on Rust Control and Prevention;
expenditure. Steel siding generally has a higher initial cost than aluminum and other siding options. However, it lasts longer than alternative cladding, so its use can be cost-effective in the long run. Manufacturers claim that steel siding will last the life of the home, and some even offer warranties of 50 years or more, while aluminum and vinyl will require expensive replacements. However, the home's resale value may be reduced if buyers are concerned about purchasing a building with an unusual type of siding;
difficult installation. Steel is heavier than aluminum and assembly is more laborious. A special and expensive blade must be used to cut the steel, and the process is very noisy, which can disturb neighbors if the steel needs to be cut on site. Installing steel siding is rarely a DIY project; it requires an experienced plumber. Repairing a damaged segment requires replacing the entire sheet, which is much more difficult and expensive than replacing a single piece of vinyl; and
energy inefficient. Compared to non-metallic cladding, steel easily transfers heat between the living area and the exterior, increasing energy costs and indoor temperature regulation. An energy-efficient design using steel cladding requires the installation of insulating material under the steel. Steel is also a non-renewable resource and its production requires a relatively large amount of energy.
There is a lot of steel siding in the Cincinnati area. LiteHouse Commercial inspectors are trained to identify defects in steel siding and will report on areas in need of maintenance or repair.
댓글